Modular sheep delivery units prove their value
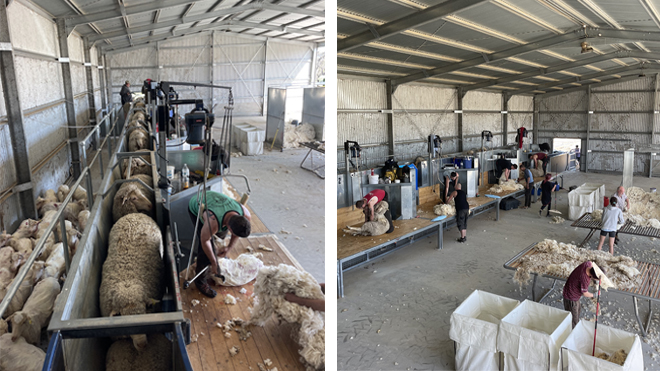
One of Australia’s largest woolgrowers, Ian Shippen of Banyandah Pastoral Co in the Riverina of NSW, was thankful to use seven AWI modular sheep delivery units late last year when flooding stranded many thousands of his sheep.
One of Australia’s largest woolgrowers, Ian Shippen of Banyandah Pastoral Co in the Riverina of NSW, was thankful to use seven AWI modular sheep delivery units late last year when flooding stranded many thousands of his sheep.
Ian, Camilla, Will, Emma and James Shippen of Banyandah Pastoral Co run a huge self-replacing Merino operation across 105,000 hectares, the majority of which is situated at Moulamein in the Hay Plains of NSW.
The average annual rainfall there is 330mm but in November last year there was unprecedented flooding which stranded many of the Shippens’ sheep and put half of their usual shearing sheds out of action. This was terrible timing, with the gigantic annual task of shearing 55,000 grown sheep and 40,000 lambs having only recently begun.
“It was a pretty difficult shearing this one! We were inundated with flood waters that probably only happen about once every 50 years in our country,” Ian said.
“We usually shear in about four different sheds, but due to the flooding, we had to truck around 30,000-40,000 sheep. In the end, I rang AWI in desperation saying we had to do something.”
Ian says that his dire situation was helped enormously when AWI organised for five modular sheep delivery units owned by AWI, and two more owned by Haynes Engineering, to be made available for him to use.
“AWI got some modular shearing units delivered to us at one of our places that wasn’t too badly affected by floodwater. We turned an existing hay shed, sized about 30m x 18m, into a shearing shed with a set of yards in about three weeks. We cemented the floor and put in seven modular shearing units which worked really well.”
The size of the existing hay shed meant that the seven modular units were configured into an ‘L’ shape, with a fabricator creating a corner to allow the sheep to flow. The Shippens have since shorn approximately 15-20,000 sheep through the system and have confirmed their intention to purchase the modular units from AWI and Haynes Engineering as they now have a fully operational shed at a fraction of the cost of other designs.
“I think the shed ran very well. We hadn’t had a lot of time to think about how best to adapt the hay shed into a shearing shed and I’d maybe change a few little things, but conceptually it worked well. We were surprised how it took limited effort to get the sheep to flow up into the race and once in the race they ran well. I was very happy with it,” Ian said.
“We had a crew of seven shearers doing about 900 sheep per day. The professional shearers that we had – those who see shearing as a career – they really warmed to the sheep delivery units; they thought it was a fantastic concept. They reckoned it was worth about five or six sheep per run better in their tallies. These are people doing about 35 a run so it was a pretty big increase in production.
“As an industry, we have to embrace innovations like the AWI sheep delivery system because it means less energy used by the shearers.”
- Ian Shippen, woolgrower
“The shearers also said they felt a lot better and less tired at the end of the week, so they really embraced it. I’m no spring chicken, I’m 57, and I picked up a handpiece a couple of times myself and did it easily. As an industry, we have to embrace innovations like the AWI sheep delivery system because it means less energy used by the shearers.”
Ian says that although the flooding combined with the lack of shearers made their shearing a very drawn-out affair this time around, he is a true wool enthusiast who revels in watching his 21-micron Banyandah Pastoral wool clip be shorn and packed into more than 3,600 bales.
“We started shearing in October and it took until February to finish. But a big thank you to AWI this year because we were in all sorts of trouble at the beginning. It was a tough few months, but I am really positive about the future of wool. I think it’s a fantastic product and am definitely going to stick with it.”
More information: Hear from Ian is Episode 241 of AWI’s The Yarn podcast at www.wool.com/podcast.
What are the AWI sheep delivery units?
The AWI sheep delivery unit in action. The manual version is featured in this photo; the automatic version is in the photo below.
The AWI sheep delivery units provide a system that delivers sheep directly to the shearer, eliminating the time and energy that shearers spend on the catch and drag. It also minimises the chance of injury to the shearer from the dragging and twisting movements.
The design focuses on a ‘modular’ concept in which portable singular shearing stands can be joined together to make a multi-stand shearing platform, which can be stored away after use. Each modular unit holds three sheep in a race at the back of the unit. A dummy pen is fitted onto the end of the race to assist with the flow of sheep.
The automatic module contains a pneumatically powered delivery section that, at the press of a button, moves out from the race and then tilts the sheep into a position suitable for the shearer to then easily retrieve the animal.
There is also a manual version which is very similar to the automatic module’s race, except that in the race there is a simple spring-loaded gate, in place of the automatic delivery section. The shearer simply opens the gate and collects the sheep from the race and manoeuvres the sheep the metre or so to the centre of the board before starting shearing.
For both modules, an angled chute allows for simple release of the shorn sheep underneath the race – again without significant dragging or twisting.
The potential benefits for woolgrowers and the industry of the AWI sheep delivery unit include:
- increased attraction and retention of shearers to the industry
- decrease in shearer injuries
- improved productivity for workers
- cost effective option when upgrading infrastructure
- provides an avenue for multipurpose sheds.
There are several companies across Australia manufacturing a sheep delivery system based on the AWI designs, including:
- Haynes Engineering of Naracoorte SA produces an automatic and a manual modular race delivery system. 08 8762 2744, haynesengineering.com.au
- Commander Ag-Quip of Albany WA produces an automatic and a manual modular race delivery system. 1800 655 033, commanderagquip.com.au
- Stockpro of Condobolin NSW produces a manual modular race delivery system.1800 354 415, stockpro.com.au
- ProWay of Wagga Wagga NSW produces both fixed and modular manual race delivery systems and provide a full design and construction service incorporating the modules. 1300 655 383, proway.com.au
- Kyabram Steel of Kyabram Vic manufactures the manual modular race units. 03 5853 1554, kyabramsteel.com.au
- RW Engineering of Darkan WA are developing and manufacturing the sheep delivery system. 08 9736 1166, rwengineering.com.au
Shearing & Sheep Handling Innovation on display in South Australia
The AWI sheep delivery unit on show at the Shearing & Sheep Handling Innovation & Demonstration Day. The automatic version is featured on the left of the photo.
AWI and PIRSA on 24 February held a Shearing & Sheep Handling Innovation & Demonstration Day at Jamestown in South Australia. It gave woolgrowers a chance to see demonstrations of commercially available options for mobile, upright and adaptable wool harvesting alternatives – including the AWI sheep delivery unit (pictured above) – as well as a range of sheep handling equipment and sheep yards.
The Jamestown event followed the successful Wool Harvesting Innovation Demonstration Days held by AWI last year at Conargo in NSW and at Gairdner in WA. The AWI sheep delivery unit was also showcased in action at Kangaroo Island’s Farming Tool & Tech Field Day in early March, which also generated plenty of interest.
Kondinin talks sheds, yard design, sheep handlers
A quiet revolution has been taking place in recent years across sheep yards and shed design as well as the rapid development of the myriad of sheep handlers that are now on the market. These are all working to make sheep work easier, but which one is right for you?
Ben White from the Kondinin Group talked through the important considerations with AWI’s National Extension Manager, Emily King, at the AWI Sheep Handling Innovation and Demonstration Day in SA recently. Hear from Ben is Episode 242 of AWI’s The Yarn podcast at www.wool.com/podcast.
This article appeared in the June 2023 edition of AWI’s Beyond the Bale magazine. Reproduction of the article is encouraged.