Aussie Merino knitted on the Aussie farm
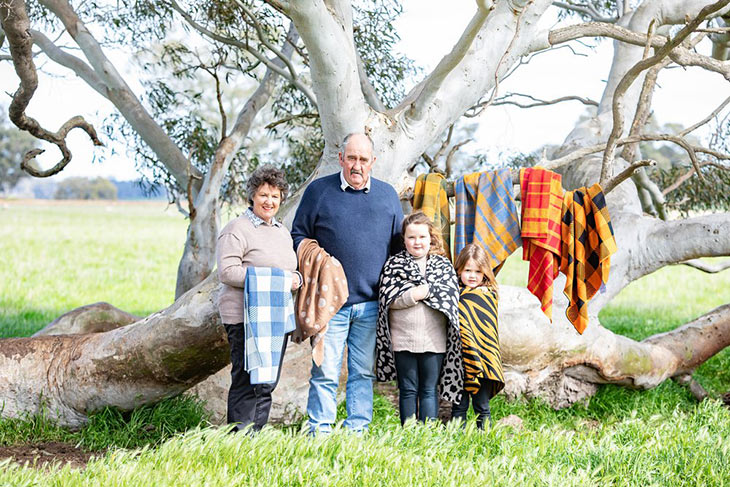
Sheep and wool farmer Sue McClure has purchased and set up a commercial-sized Shima Seiki knitting machine on her farm in rural Victoria to manufacture sustainable products made from Woolmark certified Australian fine Merino wool yarn.
Sue and Mal McClure with their granddaughters Rhianna and Madeline and a selection of blankets from Kilmaille Knits on their property in Victoria.
Sheep and wool farmer Sue McClure has purchased and set up a commercial-sized Shima Seiki knitting machine on her farm in rural Victoria to manufacture sustainable products made from Woolmark certified Australian fine Merino wool yarn.
With their children and grandchildren, fourth generation farmers Sue and Mal McClure run sheep at Pigeon Ponds near Harrow in Western Victoria. A love of wool has been in their family’s DNA for generations.
Now nearing the end of her ‘other career’ as a textile teacher at Balmoral Community College, Sue has extended her passion for knitting to a commercial level by setting up Kilmaille Knits, a business that manufactures and sells woollen knitted products direct from her farm.
“I’ve always wanted to see more wool manufactured into garments in Australia where it is grown. But last year I felt that the time was right to take a leap of faith and follow my dream to manufacture Australian Merino knitwear right here on our farm – Aussie wool, Aussie made, Aussie owned, Aussie farm,” Sue said.
The product range of Kilmaille Knits is mainly blankets and scarves at the moment, but Sue is currently working on a collection of whole garment knitwear products and she says the range will expand in the future as she becomes more skilled with her new Shima Seiki knitting machine.
“But at this stage, most of our business is custom orders for personalised blankets that include things like baby names and dates of birth, footy team slogans and property names. I do a lot of named blankets for customers in their favourite footy team colours – I’ve even done them for Essendon legends Reg Burgess and Barry Capuano!” she said.
“I check every item that is produced for quality before it is despatched, and we receive very good feedback from customers.”
The Shima Seiki Mach2Vs WHOLEGARMENT® commercial-sized knitting machine set up in the McClures’ knitting studio on their farm.
Sustainability at the heart of the brand
Sue says that as a textiles teacher, she is very conscious of the detrimental environmental impacts of the fast fashion industry.
“There is an enormous volume of clothing that is dumped in landfill, and synthetic fibres and their microfibres cause significant problems to our waterways and planet,” Sue said.
“In contrast to synthetics, wool is a natural, biodegradable and renewable fibre with many endearing qualities. Our family cares very much about sustainable farming practices and the environment in which we work and live. I also want to see sustainability at the other end of the supply chain, by wool products replacing synthetic products.”
“We are dedicated to making the best wool products that are not just a purchase, but an investment.”
Sue McClure
In July, Sue completed a short course in Circular Economy & Sustainability Strategies through the business school of the University of Cambridge.
“This helped cement the idea that what I am trying to achieve is so worthwhile,” she said. “The Kilmaille knitwear products are non-seasonal and are intended to be lifelong, reused, repurposed, repaired and recycled – thereby being part of the circular fashion economy. Even all my packaging is 100% compostable.
“I have photocopied and framed the ‘Wool is ideal for the circular economy’ article from the latest edition of Beyond the Bale. I nearly teared up when I saw that article. It’s like yes, yes, yes!
“AWI were helpful in providing me with information in general, particularly regarding wool processing and the finishing of wool, and they supplied contact details for yarn processors. They also gave me lots of sound advice about what consumers want.”
The high-tech knitting machine
After many months of planning and researching, Sue’s dream to knit Australian fine Merino wool on her own farm become a reality in September last year with the arrival of the Shima Seiki commercial scale knitting machine all the way from Japan.
“To say we were excited is an understatement!” said Sue.
“We purchased the machine in May through textile equipment importer Ramsay McDonald Australia Pty Ltd in Melbourne. The machine arrived on a large steel pallet, and we needed a forklift, pallet lifter and several strong men to get it positioned into our garage that we had converted to a knitting studio. Rod Murray from Ramsay McDonald came down to the farm and was indispensable in helping us get it set up.”
The Shima Seiki machine that Sue purchased is a WHOLEGARMENT® machine which means that its products are knitted in three dimensions without seams. Another advantage is that it uses exactly the correct quantity of yarn, thereby resulting in less yarn wastage than traditional manufacturing.
“This machine can use yarn of a weight that is needed to make the type of garments, blankets and throws that I want to knit. It can knit jumpers up to 3XL and blankets just over two metres wide,” Sue added.
“I had no prior experience knitting with an industrial machine, but after a week’s instruction from Rod and lots of support along the way, I felt confident doing basic knitting. I am continuing to undertake training and my skills have really come along.
“I also purchased the Shima Seiki Apex design program which enables me to produce a virtual 3D image of a garment.”
A top-quality investment
Aside from the Shima Seiki knitting machine and software, supplementary technology was also needed before production could get under way.
“Other things we needed were an industrial steam press imported from Italy, an air compressor for the knitting machine and steam press, a generator as our solar panels are insufficient to drive the boiler in the steam press. The total spend including the knitting machine was close to $300,000 before the yarn.”
Sue says that she is totally committed to using the best Australian Merino wool yarn she can source and uses Woolmark-certified yarn.
“We use Tollegno 1900’s Harmony range of extra fine Merino yarns. It is Woolmark certified, RWS certified and traceable right back to the point of origin through a supply chain that makes the gentlest footprint on the environment,” she added.
More information: www.kilmaille.com.au
This article appeared in the March 2022 edition of AWI’s Beyond the Bale magazine. Reproduction of the article is encouraged.