Digital printing - Transforms designing with wool
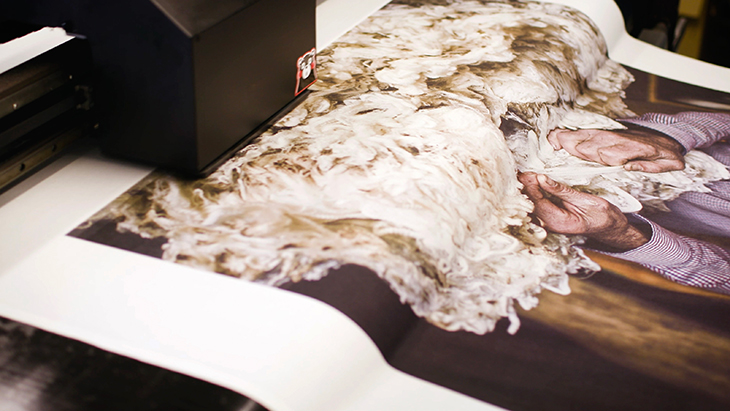
New technologies have enabled the digital printing of intricate and near-photographic designs on wool fabrics, thereby increasing design opportunities and markets for wool.
Wool fabric being passed under the head of a digital printer at Think Positive in Sydney.
New technologies have enabled the digital printing of intricate and near-photographic designs on wool fabrics, thereby increasing design opportunities and markets for wool.
BENEFITS OF DIGITAL PRINTING
- Shorter production lead times
- More flexibility in design
- No minimum order quantity
- Environmentally friendly dye
- Excess dye is recycled
- Less water
Digital fabric printing involves using inkjet technology to apply colour dyes simultaneously to a specially prepared fabric surface. In contrast to traditional print methods, digital printing is quick and personalised. The technique allows for printing on smaller lengths of fabric, lessening demand for water, chemicals and textile waste.
Designers are increasingly taking up the technology. For instance, the winner of the Karl Lagerfeld Award for Innovation at last year’s 2020 International Woolmark Prize, BODE from the USA, used digital printing in her winning designs – see image. BODE utilised the support of pioneering digital printing company Think Positive which is a trade partner of the International Woolmark Prize.
Think Positive is an internationally renowned innovator in digital direct-to-fabric printing, with amazing expertise for printing on wool as a leading luxury fibre. The company was set up in Sydney 37 years ago and now also has a studio in London and print facilities in a refurbished mill in the historic textile town of Macclesfield in Cheshire.
A digitally printed fabric sample at Think Positive in the UK of the design that was used by BODE in her collection at the 2020 International Woolmark Prize at which she won the Karl Lagerfeld Award for Innovation.
Other designers involved in International Woolmark Prize that the company has worked with include Jacinta James from Australia, Daniel Fletcher from the UK and GmbH from Germany.
“Digital printing onto textiles is the biggest breakthrough in fabric decoration technology in the past 8,000 years,” said Think Positive’s director of business development, Emilie Cacace.
“Our fabric printers are like sophisticated larger versions of desk top ink-jet printers, but instead of printing onto paper, they can ‘print’ directly onto rolls of specially prepared fabrics.
“We can print on a large range of wool fabrics: woven and knits in varying weights, wool blends like wool denim, and even wool velvet and wool fur thanks to AWI helping us experiment and work with new and innovative qualities. The results are really exciting.”
Digital printing by Think Positive on lightweight Italian wool twill in the new Spring/Summer 2021 collection of Melbourne-established and Hong Kong-based designer Vincent Li. “We did digital printing on wool for the first time,” Vincent said. “We used a lot of wool in our collection. It is a sustainable fibre and suitable not only for winter, it is perfect for summer as well.”
Think Positive has digitally printed on wool for world famous brands, such as Vivienne Westwood, and continues to receive enquiries and regular interest regarding printing on wool. The company has had its fabrics included in AWI’s sourcing guide The Wool Lab.
“Think Positive is an example of how important it is for AWI to collaborate with industry,” said AWI General Manager for Processing Innovation & Education Extension, Julie Davies.
“Digital printing offers within the industry so much flexibility with multiple benefits such as fabric sampling options, lower minimums, shorter lead times, endless design and colour options, and most importantly amazing technical capabilities for heightened print quality resulting in dynamic products.”
More information:
www.woolmark.com/digital-printing
HOW DIGITAL PRINTING TECHNOLOGY WORKS
Digital fabric printing is a series of processes whereby multiple water-soluble colour dyes are applied simultaneously to a specially prepared fabric surface. Instructed by a digital file embedded with colour management, customised inkjet heads travel back and forth across the fabric to distribute the dye in varying concentrations.
Step 1 – Fabric preparation
The ink used is a water soluble, modern textile dye. To stop the dyes from running and causing a blurring smudge, the fabric is first coated with a mixture of seaweed thickener, urea, salt and citric acid (lemon juice).
Step 2 – Printing
Tiny little drops of dye, thinner than a hair, are sprinkled over the fabric from eight different colour heads as the carriage passes across the fabric. Eight base colours that mix together can produce more than a billion colour combinations.
Step 3 – Heat setting
At first, the dye sits on the top of the fabric, which is then passed over a heat plate so that it is touch dry.
Step 4 – Steaming
Steaming the fabric opens up the fibres and creates a waterway into and around the fibres so the dyes can travel from the surface of the fabric into the fibres, forming bonds and giving the fabric permanent colour, image and design.
Step 5 – Rinse coating
Next, having done its job, the coating solution is washed out. The result is a decorated fabric that retains its original feel and texture that can be made into garments, curtains, upholstery, scarves or, cushions – the possibilities are endless.
This article appeared in the March 2021 edition of AWI’s Beyond the Bale magazine. Reproduction of the article is encouraged, however prior permission must be obtained from the Editor.